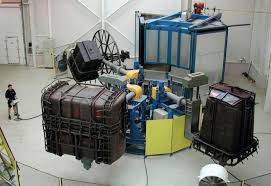
In terms of creating plastic material components, there are a number of methods readily available. One of the more well-liked and flexible strategies is rotational molding. This revolutionary process allows manufacturers to make complex, hollow plastic-type material items of virtually any design or sizing. The procedure involves placing a hollow mold in a big oven. The mold is then rotated on two axes while becoming heated up, creating the plastic-type material to dissolve and disperse evenly through the fungus. On this page, we will take a close look at rotational molding and how it is actually revolutionizing the way we make high quality plastics.
Flexibility
Plastics Rotomolding is widely famous for its extraordinary versatility. This manufacturing technique can be used to produce a comprehensive variety of products, including play ground products, industrial tanks, and custom made-created items. The possibilities are virtually limitless with rotational molding! Furthermore, this procedure makes sure that the final item carries a clean and consistent feel, which is necessary for the ultimate expertise of the item.
Cost-Effective
Unlike classic molding strategies, rotational molding is a comparatively cheap procedure as it will not call for pricey molds or machinery. Moreover, given that each fungus can be used again many times, the price of generation dramatically diminishes per piece generated. This will make it a cost-effective option for companies planning to develop good quality plastic-type products without breaking their price range.
Durability
One of many essential benefits associated with rotational molding is the reliability of the conclusion product or service. Since the polymer or resin material used along the way is warmed up and slowly cooled, the very last product is a lot less vulnerable to cracking, warping, or deforming over time. In turn, these long lasting plastics can stand up to tough environments, rough weather conditions, and repeated use without displaying any warning signs of deterioration.
Surroundings-Friendly
The rotational molding process makes use of natural gas, propane gas, or another nice and clean energy sources, which greatly minimizes air pollution from the environment. In addition, the materials getting used during this process of rotational molding are eco-friendly. Consequently producing high quality plastic-type material goods employing rotational molding will work for the surroundings.
Customization
Just about the most significant benefits of the rotational molding procedure is that it allows producers to generate customized products which meet up with their customers’ distinct demands. This will give the manufacturer versatility to deliver goods that clients need to have and which will inevitably lead to far better customer happiness. In addition, given that types are reusable, modifications can be made efficiently and quickly.
In short:
Rotational molding is an sophisticated producing approach which is used to produce good quality plastic-type merchandise. The flexibility and expense-effectiveness of rotational molding allow it to be the most preferred range of companies worldwide. Additionally, the reliability of the final item, combined with personalization, delivers included advantages which provide good value. The method promises you of uniform, sleek-textured products which are bound to stand up the test of your energy. With all of these rewards, you can actually understand why rotational molding has taken centre period in the area of high quality plastic-type material developing right now.